Mauritech is a young and dynamic company, specialised in the production of tailor-made mechanical parts.
The valuable experience, gained over the years of work as well as the commitment of our company’s owner, Maurizio to follow every step of the production process, has allowed us to grow and become consolidated partners of major companies, including multinationals.
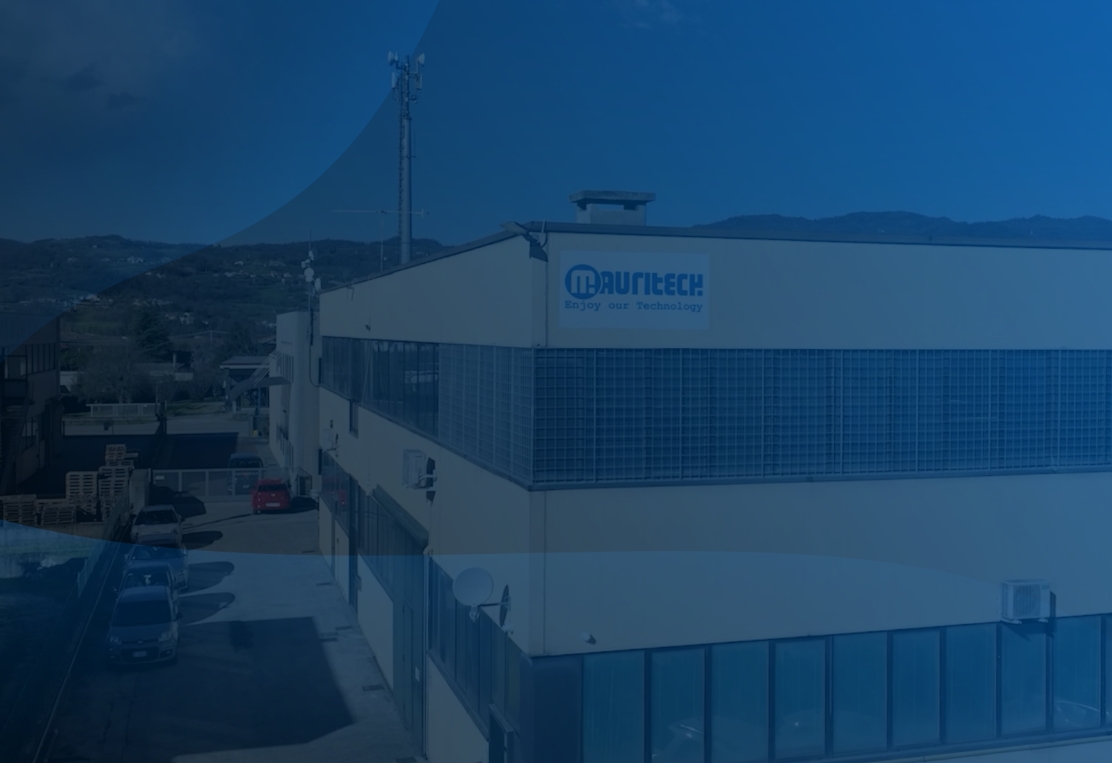
MAURITECH SRL
Who we are

Mission
Our mission is to achieve customer loyalty which can only take place through customer satisfaction.
The latter is what we strive for at Mauritech and where we want to excel in, mainly by responding to the various requests of our partners, advising and supporting them until we represent a reliable point of reference for them.
Check the video

What we do
We bring life into your components
from design to the finished product
Early on, in the proposal phase, a detailed study will be conducted starting from the raw materials, continuing on through the various processing phases. Each step is carefully and professionally evaluated in order to guarantee the quality, requested by the customer.
As soon as we receive your order, we initiate the planning process, after which we proceed with the procurement of the raw materials.
At this point, we manage to have a clear vision on the number of hours we need to devote to the production of your component.
A job order is then generated for the actual production of the related part. This includes a technical data sheet, on which all of the necessary criticalities and tolerances that need to be respected are reported on.
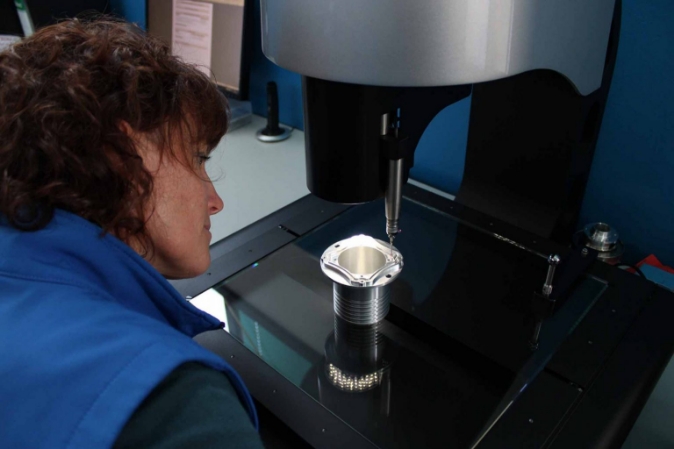
During the set-up, we study the best way to optimize the production process in its entirety,
in order to ensure you the best price in compliance with the required and expected quality standards.
The actual production only starts after dimensional and visual checks have been carried out by our quality manager,
followed by further control mechanisms as well as monitoring the progress of the job order.
As mentioned earlier on, diligent attention is also paid to the packaging phase of the components.
In fact, the most suitable packaging is chosen in order to preserve the characteristics of the component and to overcome
any damage due to transportation. To reassure our customers that components arrive unscathed at their destination,
we carefully select our couriers and entrust the most delicate shipments to a designated courier.